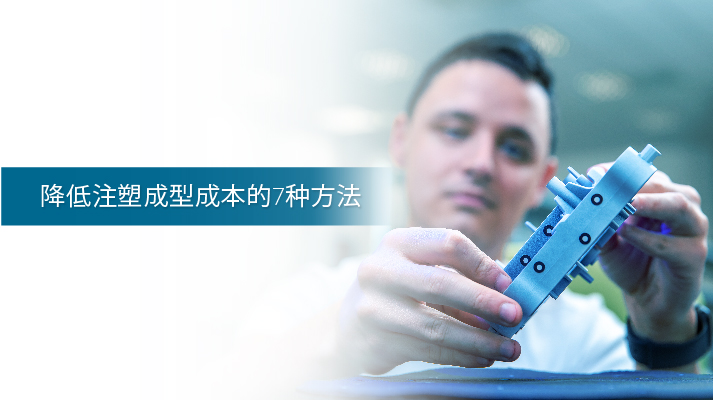
注塑成型是一种高效的制造方式,但是通常会产生大量浪费,其中包括效率低下,工作失误,注塑机损坏和停机以及高废弃率,等等。以下是降低注塑成本的7种方法,可以帮助提高注塑成型的利润。
1. 降低风险与质量成本
降低风险和质量成本的方面通常是被动的,而不是主动的。之所以发生这种情况的原因是,注射成型工艺流程伴随着不可预见的异常变化,使其很难预测。由于交付的产品不合格,这使我们面临意外的风险和费用。
其实有更好的方法。首先使用科学的成型原则来开发可重复的稳定的工艺。在使用传感器和成型技术开发出工艺之后,即可监控注塑成型中各种常见的注塑缺陷,以确保为你的客户提供100%的质量保障。
我们经常可以见到这样的情况:一台注塑机已经运行了数周,工艺技术人员仍需不断进行调整。这时产品质量总是出现缺陷,因此我们必须调整工艺来改善,同时隔离可疑品,从中分选出不良的产品,并粉碎,重新成型。
最糟糕的情况就是,我们已经将其中一些产品发给了客户,这样就不得不提醒客户产品出现的问题。出现这种情况时,成本是极高的。没有根据科学的成型原理开发和记录可靠的工艺,我们的技术员就只能把宝贵的时间白白耗费在调整工艺,以期望这样生产出合格的产品。
一旦发生产品缺陷,技术人员会再次被要求调整注塑机以解决问题,并且不确定问题是否会再次发生。这时我们必须决定如何处理产品,分选或返工可能需要几天甚至几周的时间,而且极少100%有效。更不用说这是一项不增值的任务。
如果这些产品已经发送给客户,付出的代价可能是丢掉生意。如果我们在一开始就花时间创建并记录一个可以重复生产高质量产品的工艺,就可以避免出现这种情况。使用模腔压力传感器来监测生产工艺可以实现更高级别的质量控制。想象一下,在模具打开之前就知道产品是否合格,并能够自动分选产品。
2. 通过自动化提高效率
借助成型技术和培训,可以实现多个生产领域自动化,帮助提高劳动力效率。产品抓取、产品堆放与托盘包装是三种有用的自动化方法。工艺控制技术可以实现产品自动分选和报警,以便让你知道工艺何时超出了公差。通过提供数据,你可以更快地确定根本原因,而无需相互指责,从而进一步提高了效率和准确性。你可以停止故障排除,并开始解决问题。
想想没有自动化的工厂中的流程。在一步步成型制造过程中,我们需要从模具中取出产品和流道,将产品有序放置起来,并包装,然后将最终产品进行托盘包装。在这个流程的某个环节,你可以还需要添加一个装配步骤,这将增加额外的劳动力,占地空间和时间。
如果这些流程全部由人工完成,那么流程的效率总会不尽相同。如果我们仅考虑从模具中取出产品这一个环节,即使是最精准的操作员也会有时间的波动,造成周期时间的变化,从而导致产品质量的不稳定。这种波动将在过程中的每个环节中累积。
当我们开始自动化流程时,我们开始去除这些波动,提高效率,改进质量,并增加可用的空间。质量自动化 — 通过工艺监控,视觉系统,或在线尺寸验证 — 可以确保我们的客户再也不会收到有缺陷的产品。
3. 提高工艺波动的意识(减少废弃品)
通过迅速地知道工艺何时发生了变化,你可以更快地解决问题。这意味着会减少废品数量,从而提高注塑机的利用率,并降低废弃成本。你可以通过工艺控制软件,模腔压力监控和培训来实现这一目标。
在制造过程中,始终存在固有的质量成本。这种成本可能会在生产的后端产生,即在将产品交付给客户之前,使用宝贵的资源和时间检查产品。这样造成的问题是我们从来没有得到一个固定的质量成本。随着生产的变化,分选产品的时间和所需的员工数量也随之变化。
如果存在员工流失的问题,那么还必须投资新员工的培训,让他们学习如何分选不合格产品。通过确保所有技术人员都接受相同标准的培训,你可以主动减少或消除不合格品,而不是被动应对,或者防止由于技能水平低,设置的成型工艺其工艺窗口太小或没有工艺窗口造成的高报废率。
另一种考虑质量成本的方法是在前端。通过将质量构建到流程中,并监控整个周期的质量,我们就能够检测出在何时发生了工艺波动。例如,如果我们知道材料大范围的粘度变化将会导致质量问题,那么我们可以使用工艺监控工具来检测粘度的变化。在这一点,工艺可以重新回到中值以重新制造高质量的产品。
4. 购买宽规格树脂
性能变化较大的树脂更便宜,但是对于公差严格的产品,很难确保或维持产品尺寸。这无疑增加了可变性,从而导致废品率上升。但是如果我们使用DECOUPLED MOLDING®(分段成型)技术和模腔传感器,这将可能是一次成功的冒险。
你是否常常见到这种情况:连续几天生产良品,然后突然产品出现飞边。为了解决这个问题,工艺技术人员降低了填充速度。数小时后,出现了短射。为什么本来一切运行良好,然后突然就出现了飞边?答案很可能是粘度。
粘度通常可以上下波动30%,即使采用Decoupled II成型工艺,也很难生产出合格产品。为了确保每个周期都制造出相同的产品(或者至少尽可能地接近),必须使用模腔压力传感器来控制工艺,并最大限度地减少材料粘度变化的影响。
5. 缩短周期时间
你可以利用科学的成型技术和DECOUPLED MOLDING®(分段成型)技术来优化锁模力/顶出动作,填充时间,补缩时间,保压时间和冷却。你可以用一个较小的料垫来成型出良品。
适当规格的模具温度控制单元或模温机,也有助于缩短周期时间。80%的成型周期时间用于将产品从熔体温度冷却到脱模温度,使产品足够坚硬以能够承受顶出力,并保持产品尺寸稳定性。如果没有足够的冷却水流量,那么将产品冷却到正确温度的能力就会受到影响。所做的工作就只能是让产品在模具中停留更长的时间,花费更多的钱。
在项目开始时评估产品厚度是确定周期时间的第一步。质疑产品的厚度以及它如何影响周期时间和产品性能,是非常重要的。通常,我们发现产品是按这种方式设计的,因为“我们一直都是这样做的”。你可以想象,这样成本可能极高。科学和模拟有助于预测设计的成功,因此我们不再需要成型产品进行测试便可获得结果。确保适当的产品设计只是降低周期时间的一个例子。
6. 制造更高效的模具
简单地说,一个模具既是一个压力容器又是一个热交换器 — 在模腔内总是会有压力损失。然而,在大多数情况下,从浇口到模腔末端的压力损失越低,产品发生质量问题的可能性越小,如翘曲,缩孔,缩痕,短射,或尺寸波动。
要使塑料流动,我们需要加热,但要顶出产品,我们需要排除一部分热量。为了制造出高效的模具,确保冷却水路的正确设计是至关重要。我们还需要选择一种传热良好的金属,但也需要抵抗如材料的磨损(特别是带有玻璃或碳纤维填充的材料)。最后,该工艺必须设置湍流,以确保模具能够快速达到热稳定状态,并在长期生产运行中保持这种稳定。
你还可以通过增加模腔来提高模具效率。单腔模具的波动量最少,然而,一次制造一个产品的成本非常高。如果采用更高的模腔数量,则可以在相同时间内制造更多的产品。可以容纳多少个模腔存在一些限制,包括产品质量,模具和注塑机的间距以及验证要求。
另一种提高模具效率的方法是制造家庭模具,在同一个模具中包含不同的产品几何形状。这可能很困难,因为四个塑料变量在每个模腔内都不同。但是,借助工艺控制软件和模腔传感器,你可以通过针阀浇口单独控制每个模腔。
7. 降低模具转移成本
工艺开发应用程序确保您可以快速和轻松地将模具从一台注塑机转移到另一台。当模具转移时,会自动生成注塑机的设置条件表,所以你可以从第一模就制作出良品。这些曲线可以用于任何注塑机,只要注塑机能够提供足够的流量,压力,温度和体积。或者,如果不使用模拟,我们也可以生成模板,并将它们转移到任何有能力的注塑机上。
不必创建专门的转换工具,也不必为每台新注塑机重新创建工艺,从而节省时间、精力和资源。